Magnesium Alloys
Magnesium (Mg) is the lightest metallic structural material and thus one ofthe most promising candidates for lightweight applications ranging from aerospace and automotive to biomedical technologies. Its attractiveness stems from the considerably higher specific strength and bending stiffness achievable with Mg alloys than even with aluminum, which is currently the prevalent metal for lightweight applications. One of the evident benefits of lighter structural parts are the significant savings in fuel consumption and thereby the reduction of greenhouse gases. Moreover, Mg is highly bio-compatible, rendering it a desirable candidate for medical applications. Lastly, it is available in abundance in the earth's crust, making it not only a lighter but also a less expensive alternative to e.g. aluminum. Unfortunately, Mg poses severe challenges to materials scientists and engineers when it comes to its usage and processing, which is why we investigate the mechanics of Mg and Mg alloys via multiscale simulations.
The material properties of metallic parts made of Mg (and its alloys) depend significantly on the processing route. Deep drawing and cold or hot rolling are two of many strategies pursued to turn Mg into products, and the specifics of each process (including the temperature, loading rate, and more) have a considerable influence on microstructural mechanisms and thus on the resulting microstructure and, ultimately, the resulting properties. We therefore develop models that simulate the evolution of microstructure based on the process parameters, thus allowing us to understand and predict the resulting material properties and to tune those according to the specific requirements of an application. Since the treatment and processing of Mg alloys often includes thermal aspects, our extended crystal plasticity and phase field models must account for temperature-dependent material behavior.
For the prediction of microstructure evolution, we develop and employ computational homogenization techniques to simulate - through physics-based multiscale modeling - the intricate microscale evolution mecahnisms as well as the effective, macroscale properties resulting from a particular microstructure. From a numerical perspective, periodic homogenization allows us to observe the formation and development of microstructure, while seamlessly providing a route for obtaining effective constitutive response at the level of a pepresentative volume element (RVE) on the mesoscale. This provides, e.g., the effective stress-strain behavior of polycrystalline magnesium at different levels of temperature and for different load histories.
With our collaborators at Johns Hopkins University and the California Institute of Technology, we investigate the microstructural evolution of magnesium alloys under severe plastic deformation. We seek to find out how macroscale process parameters influence the evolution of microstructure, which is significantly affected by the mechanisms of recrystallization and precipitation. We integrate those into an extended crystal plasticity framework, which accounts for plasticity by dislocation slip and by deformation twinning (in an average, mesoscale sense). Using a spectral formulation for the numerical setup allows us to capture local variations across RVEs of high resolution, detailing regions of high slip and twin activity or dislocation and precipiate distribution. Simulated predictions are compared to electron backscatter diffraction microscopy (EBSD) images, which serves both model calibration and validation.
Owing to its hcp crystallography, deformation mechanisms of magnesium involve both deformation twinning and plastic slip. To describe and understand, and ultimately to predict the mechanical response of Mg and Mg alloys, our theoretical-computational framework captures the intricate interaction mechanisms of twinning and slip and thus provides a basis for
- understanding microstructural deformation mechanisms,
- describing the resulting effective macroscopic mechanical response,
- predicting effective mechanical behavior,
over wide ranges of ambient conditions (e.g. from ambient up to high temperature) and loading conditions (including high strain rates such as during high-speed impact). Our objective is two-fold. First, we aim to understand the link between process conditions and resulting microstructure. Second, we aim to understand the influence of microstructural characteristics (such as grain size, twin spacing, texture, composition, and defect distribution) on the observable material performance. Overall, this leads to a chain from processing to microstructure to properties, whose understanding is key to utilizing Mg and Mg alloys in technological applications.
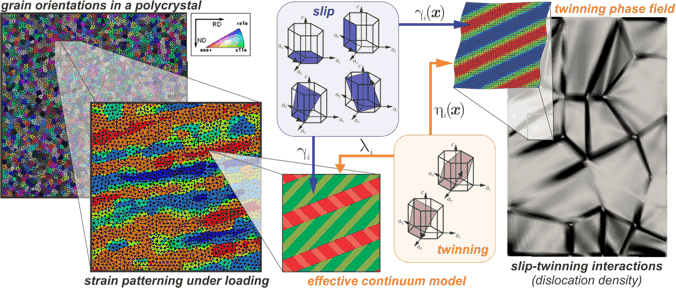
On the one hand, we have combined a phase field model (that describes the deformation twinning process) with a gradient plasticity description (or, continuum dislocation theory, which models dislocation activity based on a continuum dislocation density tensor that can be uniquely linked to the plastic slips on all active systems). Due to its nonlocal formulation, this model is size-aware; that is it is well suited to describe intrinsic size effects such as those arising from dislocation pile-ups within grains as well as between twin boundaries. The graphics below illustrate an example of a micro-twin nucleating out of an untwinned crystal, showing the distribution of both the dislocation density and the twin phase. The twin boundary accumulates dislocations as the twin phase expands.
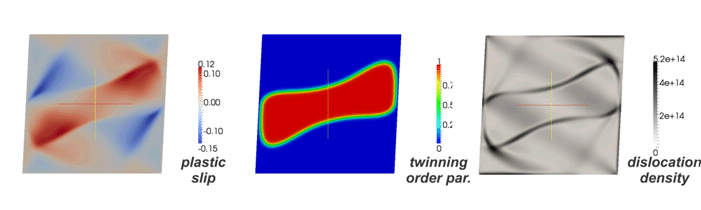
More recently, we have developed and implemented new models for Mg of extended crystal-plasticity type to account for the disparate scales involved: twinning is commonly observed at a much smaller length scales (typical twin spacings in Mg can be as low as several nanometers) than dislocations (which live on the polycrystals' mesoscale of many microns). The crystal plasticity model decouples the length scales by finding an effective description for twinning in terms of twin volume fractions. The model has been calibrated and validated by comparison with experimental data for single- and polycrystalline Mg, and it gives reasonable predictions not only of the resultant stress-strain response but also of the microstructure evolution in polycrystals, the dominant slip/twin modes, and the underlying texture development.
We use the crystal plasticity model, among others, to predict the texture evolution in polycrystalline Mg samples produced by Equal Channel Angular Extrusion (ECAE), which admits comparison to experimental data and is a prime processing route taken by our collaborators. Importantly, the severe plastic deformation during ECAE (similar to hot compression) gives rise to permanent microstructural changes associated with recrystallization and recovery. We therefore developed a stochastic extension of our modeling framework to include dynamic discontinuous recrystallization (with continuous recrystallization also becoming visible in simulations). To this end, we combined our extended crystal plasticity setup with a Field Monte-Carlo-Potts ansatz to describe the nucleation and growth of new grains at the mesoscale, based on statistical arguments and based on the local energetics within a sample (high concentrations of stored energy giving rise to a high propensity to grain nucleation and, again, reduction in energy being the key driver for grain boundary motion). The resulting model predicts dynamic recrystallization in Mg, displaying - as shown below - recrystallization waves in the stress-strain response along with nucleating and growing grains within a polycrystallin RVE.
We constantly explore new avenues for modeling the microstructure evolution in Mg and Mg alloys as a function of process parameters and initial texture, and we evaluate our approaches based on accuracy and efficiency. external page We have shown for selected examples that a simple and efficient Taylor model can yield the sought simulation results in only a small fraction of the time required by fully-resolved RVE models, while still providing high accuracy.